Precision pipe production of key technologies
Home >
-
API steel pipe
- API steel pipe
- API steel casing pipe
- Casing and Tubing
- API drill pipe
- API5L steel pipe
- Oil pipeline

-
Carbon steel pipe
- Carbon steel pipe
- Welded steel Pipe
- seamless carbon steel pipe
- Petroleum Casing Pipe

-
Alloy steel pipe
- astm a 335 gr p22
- alloy steel pipe l555
- 25crmo4 alloy steel pipe
- alloy pipe a335 p11








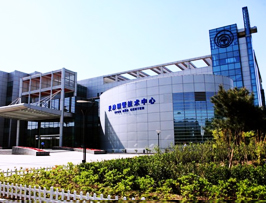
One of the Top 500 enterprises in China foreign trade
QCCO was approved as a member of “China Association for Contracting Projects Abroad “and granted a membership certificate on Sep 28,2005; “Credibility Rating AAA certificate in Foreign Trade” was granted to QCCO by China Shippers’ Association
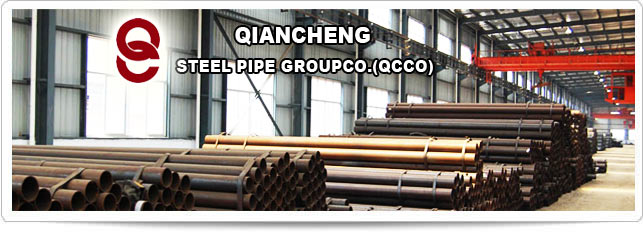
Precision pipe production of key technologies (one)
First, the raw material quality requirements:
Precision pipe of raw materials, in addition to ordinary high-frequency welded steel pipe must meet the basic requirements of raw materials, the parties must meet the following requirements:
A chemical composition:
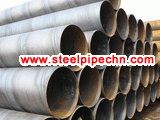
Smelting, the focus is to improve the purity of the steel, to reduce non-metallic inclusions in steel the content of sulfur and phosphorus content should be less than 0.03%, in order to meet after cold deformation processing step, the sulfur content is preferably not more than 0.02%, and therefore strict control of the chemical composition of steel. Same time to ensure the product has good mechanical properties, bending, welding and other process performance, the need to appropriately increase the number of Nb, Ni, V and other elements.
2 strip shape and dimensions:
Rolled steel should be used when AGC and flatness control system to improve the accuracy of strip thickness and flatness accuracy. But also the use of controlled cooling methods to improve the strength and toughness of the steel strip. Slitting strip width required to control the dimensional accuracy of the strip edges and burrs to no indentation, in order to improve the quality of welding.
3 steel surface corrosion:
The surface of the strip iron oxide yellow rust water of crystallization, in the welding process, the high temperature causes one of the oxyhydrogen folded, if not discharged, being present in the weld, easy to produce pores microcracks change the organizational structure and reduce plastic materials, lower elongation, so to avoid the strip surface rust.
Second, the pipe forming process:
Pipe forming process, ie welded pipe forming and sizing section pass design and tuning methods will directly affect the quality of welding and disadvantages. The traditional roll forming process for the forming process, a single radius, double radius; W reverse bending method forming pass system, with two rollers, three rollers, four or five rollers squeeze rollers roll, two rolls or four rolls sizing to ensure that the forming quality. Such traditional roll forming process, mostly for the pipe diameter less than φ114 mm units. American cage roll forming process, VAI CTA forming technology, Japan Nakata FF or FFX flexible forming technology and so on, after forming the weld shape and good surface quality have a better guarantee for more specifications wide welded pipe mill. Various forming technology, there are different advantages and disadvantages, suitable for different conditions, according to the product mix, product use should be carefully considered in the selection of equipment to choose a different forming process technology.
In order to reduce the elastic deformation, deformation processing unit for precision pipe passes than ordinary pipe passes a corresponding increase 2 to 3 times. Arrangements in the deformation, deformation angle should be reduced initially, to ensure a stable bite into the middle curved angle appropriate to increase the rear deformation appropriate to reduce, increase distortion passes just to reduce deformation force, but also to a release strip surface stress opportunity to increase the surface stress gradient slowly to avoid cracks. In the adjustment process, we must first ensure that the vertical centerline of each pass unity to the center as the base axis, identify the location and size of the middle set in the horizontal position, shall be in accordance with the process arranged to form uphill (down line) flat straight lines, can not appear curve beating. In the absence of wear with front, you should adjust the shape of the rack hole, measuring dimensions of each pass, to ensure product stability into the rack. In the adjustment of the force should be balanced, not forcibly deformed in a rack, ensure the lifting angle stable uniform changes.
Precision pipe production, control and adjust the welded pipe forming and sizing mill stand equipment accumulated error and roll bounce amount of the older welded pipe mill can produce precision pipe key.
Third, the weld burr formation and removal:
High-frequency current through the skin effect and proximity effect, current is concentrated in the weld is heated to a molten state, the lateral pressure-welded by squeeze rolls, the subject extrusion pressure, excess weld metal and the oxide deposited on the upper forming an outer surface of the burr; by squeezing the joint action of pressure and gravity, some excess metal and the oxide along the axial direction of the inner tube form the inner burr droop.
Glitch width is usually about 0.5 to 3 mm, the inner burr height is uneven, generally 0.2 to 0.6 mm. Individual height of up to 1 mm or more. Outer burr removal method is generally used planing, while the inner space of the small glitch in the steel tube, clear technical difficulty increases. Since the inner burr exist when then drawn or cold-rolled steel finishing when the pipe inner surface cracks, folds or scratches. So for precision pipe, no clear burrs can not be achieved within the inner surface quality requirements, and can not be post-processing step process.
Outer burr removal device has a planer and two planer type, with a planer tool to shut down, but with two planer clear the glitch, ATC can be no downtime.
Technical difficulties within the burr removal, due to a special unit within the burr inside the pipe, the working environment is poor, invisible, intangible, it is subject to strip accuracy, precision equipment unit, forming process, the weld shapes and other effects, often can not be guaranteed. Foreign data reports, bore 14 mm or more in the pipe can be removed within a burr, actually bore 25 mm below the inner burr removal very difficult. Domestic technology generally bore 50 mm larger than the diameter welded steel pipe can be cleared within the burr.
Within the burr removal is usually clear in a continuous pipe production line can also be used off-line method to clear.
Within the burr removal methods, mainly in the following ways:
Cutting method: This method is to use a fixed blade inserted into the tube or rotary cutting head for cutting the burr.
Rolling method: This method is the use of the rolling device inserted into the tube, plastic deformation of the inner burr, burr height within reach thinning effect.
Oxidation: Steel pipe welding begins, using jet aeration nozzle welds inward flow of oxygen, the use of weld heat, so that the inner burr accelerated oxidation, and in the air flow out of the next shedding.
Drawing France: Steel tube through the mold, the floating piston ring blade action, clear tube inside burr.