hot rolled 12cr1movg steel pipe
Home >
-
API steel pipe
- API steel pipe
- API steel casing pipe
- Casing and Tubing
- API drill pipe
- API5L steel pipe
- Oil pipeline

-
Carbon steel pipe
- Carbon steel pipe
- Welded steel Pipe
- seamless carbon steel pipe
- Petroleum Casing Pipe

-
Alloy steel pipe
- astm a 335 gr p22
- alloy steel pipe l555
- 25crmo4 alloy steel pipe
- alloy pipe a335 p11








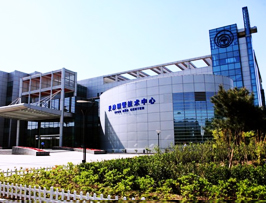
One of the Top 500 enterprises in China foreign trade
QCCO was approved as a member of “China Association for Contracting Projects Abroad “and granted a membership certificate on Sep 28,2005; “Credibility Rating AAA certificate in Foreign Trade” was granted to QCCO by China Shippers’ Association
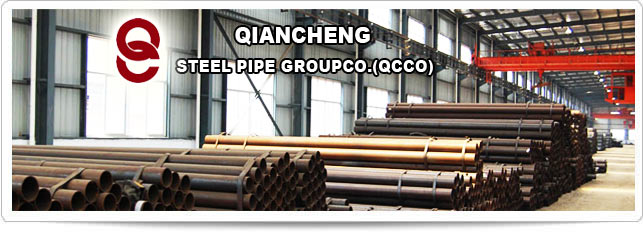
1. ionospheric
The defect characteristics: located in the inner surface of the 12cr1movg steel pipe longitudinally distributed, was raised spiral separation or rupture bulk metal-like sandwich.
Reason: material adverse caused by non-metallic inclusions, residual shrinkage or severe osteoporosis.
2. straights folding
The defect characteristics: located in the inner surface of the 12cr1movg steel pipe longitudinally distributed, showing symmetric or single-line-shaped folding with a long pass, there are local.
Reason: poor mandrel lubrication, the mandrel surface defects or surface with the oxide scale, iron filings, pided into the channel, the inner surface of the steel pipe shortage pipe in the rolling process, too full of the rolling mill pass.
3. within the hole irregular
Defect characteristics: located 12Cr1MoVG steel pipe inner surface of the longitudinally distributed, ① one or two difference of 180 ° the wall thickening, or at the separation point of the steel pipe inner surface and the mandrel have a thick wall-shaped, also known as the inner drum package . ② steel pipe inside the park was uneven wall thickness of the hexagonal-shaped, also known as the hexagon.
Cause: inner drum color: continuous rolling reduction allocation or tension improper selection, the metal too full mandrel improper selection.
Within the six-party: Less Pass and tension parameters inappropriate choice of Zhang Less machine stand-alone rack less by total reducing rates.
4 wall contraction
Defect characteristics: It is located on the inner surface of the 12Cr1MoVG steel pipe, steel pipe transverse cross-section at thinnest steel pipe inner surface depression, local thinning of the wall thickness, and severe contraction almost tear.
Cause: extending over a large rolling mill, steel pipe in the hole sidewall section, local pulled thin strip mill rack pressure adjust improper extension coefficient unreasonable distribution.
5. within the rolling scar
The defect feature: steel pipe inner surface of the vertical was a nail-like scarring, bumps or lumps folding steel tube surface indentation.
Cause: mandrel lubrication bad state, cause mandrel local wear, damage, sticky metal head badly worn metal stick, the lack of meat or large cracks perforated ears pressed against the inner wall of the steel pipe.
6. within the fold
The defect characteristics: located 12Cr1MoVG steel pipe inner surface of the end portion, topical or longitudinal was spirally semi helical or non-regular distribution of the sheet-like folded.
Cause: The perforation process mill adjust properly, immediate severe wear tube material is not good, the mandrel serious damage.
7 rolling off
The defect feature: steel pipe the surface longitudinal partial or full length of the wall was the folds of the outer concave convex or the outer surface of the steel pipe through a long vertical prescribe symmetrical obvious grooves generally linear shaped inpidually for slash.
Cause: continuous rolling shortage tube diameter is too large or too big the shortage pipe ovality, bamboo control strong enough or bad state of lubrication, the lateral displacement of the device and rolling shortage tube touch deflated, rolling mill speed error.
8. tear
The defect characteristics: located 12cr1movg longitudinally on the surface of the steel pipe tube body showed varying degrees of lateral rupture, diamond-shaped and oval-shaped holes through the tube.
Cause: rolling incoming local "spots", over rolling easily torn, defects in the form of generally diamond-shaped. And rolling the incoming temperature is low, and rolling tension is too large, rolling mill speed improper selection.
9 double seam folding
The defect feature: a pair of oblique stretching wall longitudinal cracks in the steel surface longitudinal cracks sometimes scattered in sometimes appear to symmetrical tube circumference.
Reason: perforated capillary diameter is too large or diameter irregular due to folding.
10 . Outside the fold
The defect characteristics: ① steel pipe appearance on the show regularity folding a triangular-shaped, two-seam straight, linear or irregular sheet folding single slit.
② steel pipe on the longitudinal outer presents a generally continuous or intermittent sewing pin shape or staggered 60 °, 120 °, 180 ° sewing pin shaped folded.
③ steel pipe longitudinal appearance render spiral folding.
(4) the surface of the steel pipe vertical was a to pass long punctate or short slash folding severe shifted by 120 ° of two or three.
Causes: (1) tube surface longitudinal crack or serious inclusions, shrinkage, spiral folding.
The ② tube surface cleaning adverse, sharp edges and corners or exist outside Alice skin.
The ③ punch guide plate nodulation, or punch exports mouth abrasions capillary.
The ④ rolling rolls or sheets less roll cracks or bumps.
The ⑤ Zhang Less machine roller chamfer undesirable, super life, old and new rack with improper use.
⑥ less machine steel pipe conveyor process mechanical abrasions or bruises.
⑦ Zhang Less machine roller cooling water caused Zhang reduction mill roll stick steel.
11 . Indentation
Defect characteristics: longitudinal surface of the steel pipe rendered irregular or regular local indentation, off the meat. The shape of the nuclear shape, stripe, horizontal bruised, warping like fragmentation, iron filings like.
Cause: ① Less machine finished surface of the rack roll stick with metal objects.
② scarring or other foreign body pressure off the pipe surface.
③ hot pipe bruised or scratched.
④ traverse device or sawing device bumps, embossing.
Judgment: general tube: wall thickness the ≤ 8mm indentation depth does not exceed negative deviation wall thickness> 8mmm indentation depth does not exceed the negative deviation shall not exceed1.0mm .
Boiler tube: shall not exceed half of the wall thickness of the negative deviation, a maximum of 0.6 mm .
Oil casing: the indentation depth must not exceed half of the wall thickness of the negative deviation S ≥ 10mm depth of maximum value does not exceed when S < 10mm .
12. overheating
The defect feature: steel pipe appearance appear before rough iron skin scales or scars.
Cause: heating time is too long or the temperature is too high.
13. straightening concave
The defect characteristics: steel tube outer surface showed a spiral-shaped dent.
Reason: improper the straightening roll angle adjust the amount of reduction is too large, serious straightening roller wear.
14 dent
The defect characteristics: 12cr1movg steel pipe outer surface partially irregular or regular indentation outer concave shape convex wall wall thickness did not change.
Cause: 12cr1movg pipe during transport by violent collisions or severely stamping in the cutting process, the clamping force is not properly adjusted.
Sentence off: general pipe: the dent depth shall make outside diameter beyond the negative deviation.
Boiler tubes, oil casing: dent depth shall be held outside diameter beyond the negative half of the deviation.
15. Hairline
Defect feature: in the outer surface of the steel pipe was continuous or discontinuous hairlike fine cracks, mostly spiral, the pitch is relatively large, there are approximate linear.
Reason: bad steel, subcutaneous inclusions and Blowhole tube surface clean up bad hairline.
16 Ma Face
The defect characteristics: local long pass along the steel surface presented spiky pits and grooves, some appear periodically.
Cause: less machines, rolling mill or Zhang serious roll wear in the reheating furnace, the heating time is too long or too high temperature, high-pressure water in the reheating furnace in addition to the low pressure of scales device, inpidual nozzle clogging.
Judgment: general tube: Ma surface depth of no more than half of the wall thickness of the negative deviation.
Boiler pot: Ma surface depth does not exceed half of the negative deviation, a maximum of 0.6 mm .
Oil casing: Ma surface depth of not more than half of the wall thickness of the negative deviation when S <10mm depth maximum of not more than 0.5 mm , S ≥ 10 mm depth of the maximum does not exceed0.6mm .
17. uneven wall thickness
The defect feature: steel pipe the same cross-section of the wall thickness maximum and minimum, respectively, more than the positive deviation and negative deviation or more than a nominal wall thickness of ± 8 to 10% of the ( thick-walled tube to take the upper limit of thin-walled tube to take the lower limit )
Cause: perforation incoming does not meet the requirements, the tube end face cut diagonally, tube heat centering partial, uneven heating tube, perforation equipment improperly adjusted, rolling mill equipment improperly adjusted.
18 wall thickness of ultra-poor
Defect feature: steel pipe on the same cross-section along the length direction of the steel pipe wall thickness of the ultra-poor.
Cause: mill, Less machine improperly adjusted speed improper selection mandrel wrong choice, Zhang Less thickened end has cut the net.
19 OD-tolerance
Defect feature: steel pipe on the same cross-section along the tube length direction of the outside diameter of tolerance.
Cause: Zhang Less machine pass right size processing Zhang reduction machine finish pass badly worn or pass design not, reheating furnace temperature fluctuations.
20. bending
Defect feature: steel pipe along the length is not straight, steel pipe end was goose head bent.
Cause: Zhang Less machine last few planes pass centerline dislocation. Zhang Less machine finishing pass of reducing unreasonable distribution. Unreasonable or sawing Zhang less tube cooling temperature, transportation and other causes.
21 steel pipe cracking
Defect feature: steel pipe head or partial cracking.
The Reason: steel pipe partially cooled by the cooling water in the formation of cracking and rolling or Zhang Less. The steel head top in high pressure water scales equipment being poured into "blackheads" Less machine rolling cracking.
22. brushed
Defect feature: steel pipe appearance long pass or the tube A B segment regularly or irregularly shaped lines, wire fall off or stick on the steel surface.
The causes: Zhang Less machine pass design is unreasonable, perforated capillary the continuous rolling the blank pipe outside diameter and ovality too, tubular bad, Zhang reduction machine, empty Less hole chamfering undesirable. Less machine, the empty reduction machine pass misalignment. Zhang Less machine of old and new rack mismatches.
23. abrasions
The defect characteristics: appearance in the steel pipe rendered spiral scars and other regular or irregular distribution abrasions.
Cause: steel pipe stuck in rotating equipment, mechanical equipment is not smooth and dislocation.
24 is not round shape
The defect feature: steel pipe cross-section circle.
Cause: sawing clamping force improperly adjusted Zhang Less machine finished rack and work rack position is not installed correctly, eddy current testing of finishing exports clamping device clamping force is too large, the straightening roll reduction or angle adjustment inappropriate.
25 Green Line
Defect feature: steel pipe appearance presented symmetric or asymmetric linear rolling marks along the vertical distribution.
Causes: Less machine irrational pass design, low temperature steel rolling. Zhang Less pass center misalignment dislocation. Zhang reduction machine pass ultra life, serious wear and tear. Zhang Less old and new machines pass with improper use.
26. straights
Defects special trap: vertical distribution along the pipe trench.
Cause: When the rolling temperature is low, the head stick metal scratch the surface of the steel pipe, immediate serious wear and tear. Mandrel poor lubrication or badly worn.
Judgment: general tube: outside straight no deeper than the wall thickness of the negative deviation of 90% of the deepest of not more than 1.0mm , the inside straights depth no more than wall thickness of the negative deviation does not exceed 0.6 mm .
Boiler tubes, oil casing: straights depth shall not exceed the wall thickness of 5% , the maximum does not exceed 0.4 mm .
下一篇:Steel Pipe Piling,spiral pipe pile, Large Diameter pipe foot